A tecnologia de corte de wafers, como uma etapa crítica no processo de fabricação de semicondutores, está diretamente ligada ao desempenho do chip, ao rendimento e aos custos de produção.
#01 Histórico e importância do corte de wafers
1.1 Definição de Corte de Wafer
O corte de wafers (também conhecido como riscagem) é uma etapa essencial na fabricação de semicondutores, com o objetivo de dividir os wafers processados em vários dies individuais. Esses dies normalmente contêm a funcionalidade completa do circuito e são os componentes principais utilizados na produção de dispositivos eletrônicos. À medida que os projetos de chips se tornam mais complexos e as dimensões continuam a diminuir, os requisitos de precisão e eficiência para a tecnologia de corte de wafers tornam-se cada vez mais rigorosos.
Em operações práticas, o corte de wafers normalmente utiliza ferramentas de alta precisão, como lâminas de diamante, para garantir que cada matriz permaneça intacta e totalmente funcional. As principais etapas incluem a preparação antes do corte, o controle preciso durante o processo de corte e a inspeção de qualidade após o corte.
Antes do corte, o wafer deve ser marcado e posicionado para garantir trajetórias de corte precisas. Durante o corte, parâmetros como pressão e velocidade da ferramenta devem ser rigorosamente controlados para evitar danos ao wafer. Após o corte, são realizadas inspeções de qualidade abrangentes para garantir que cada chip atenda aos padrões de desempenho.
Os princípios fundamentais da tecnologia de corte de wafers abrangem não apenas a seleção do equipamento de corte e a definição dos parâmetros do processo, mas também a influência das propriedades mecânicas e características dos materiais na qualidade do corte. Por exemplo, wafers de silício dielétrico de baixo k, devido às suas propriedades mecânicas inferiores, são altamente suscetíveis à concentração de tensões durante o corte, levando a falhas como lascamento e rachaduras. A baixa dureza e fragilidade dos materiais de baixo k os tornam mais propensos a danos estruturais sob força mecânica ou estresse térmico, particularmente durante o corte. O contato entre a ferramenta e a superfície do wafer, juntamente com altas temperaturas, pode exacerbar ainda mais a concentração de tensões.
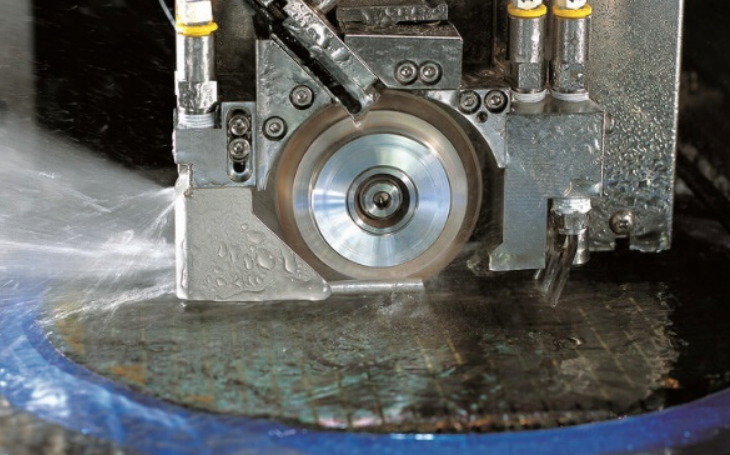
Com os avanços na ciência dos materiais, a tecnologia de corte de wafers expandiu-se para além dos semicondutores tradicionais à base de silício, incluindo novos materiais como o nitreto de gálio (GaN). Esses novos materiais, devido à sua dureza e propriedades estruturais, representam novos desafios para os processos de corte, exigindo ainda mais aprimoramentos nas ferramentas e técnicas de corte.
Como um processo crítico na indústria de semicondutores, o corte de wafers continua a ser otimizado em resposta às crescentes demandas e avanços tecnológicos, estabelecendo as bases para futuras tecnologias de microeletrônica e circuitos integrados.
Os avanços na tecnologia de corte de wafers vão além do desenvolvimento de materiais e ferramentas auxiliares. Eles também abrangem a otimização de processos, melhorias no desempenho dos equipamentos e o controle preciso dos parâmetros de corte. Esses avanços visam garantir alta precisão, eficiência e estabilidade no processo de corte de wafers, atendendo à necessidade da indústria de semicondutores por dimensões menores, maior integração e estruturas de chips mais complexas.
Área de Melhoria | Medidas Específicas | Efeitos |
Otimização de Processos | - Melhorar os preparativos iniciais, como posicionamento mais preciso do wafer e planejamento do caminho. | - Reduz erros de corte e melhora a estabilidade. |
- Minimize erros de corte e melhore a estabilidade. | - Adote mecanismos de monitoramento e feedback em tempo real para ajustar a pressão, a velocidade e a temperatura da ferramenta. | |
- Menores taxas de quebra de wafers e melhor qualidade do chip. | ||
Melhoria do desempenho do equipamento | - Utilizar sistemas mecânicos de alta precisão e tecnologia avançada de controle de automação. | - Aumente a precisão do corte e reduza o desperdício de material. |
- Introduzir tecnologia de corte a laser adequada para wafers de materiais de alta dureza. | - Melhore a eficiência da produção e reduza erros manuais. | |
- Aumentar a automação dos equipamentos para monitoramento e ajustes automáticos. | ||
Controle preciso de parâmetros | - Ajuste fino de parâmetros como profundidade de corte, velocidade, tipo de ferramenta e métodos de resfriamento. | - Garantir a integridade da matriz e o desempenho elétrico. |
- Personalize parâmetros com base no material, espessura e estrutura do wafer. | - Aumente as taxas de rendimento, reduza o desperdício de material e diminua os custos de produção. | |
Significado estratégico | - Explorar continuamente novos caminhos tecnológicos, otimizar processos e aprimorar as capacidades dos equipamentos para atender às demandas do mercado. | - Melhorar o rendimento e o desempenho da fabricação de chips, apoiando o desenvolvimento de novos materiais e designs avançados de chips. |
1.2 A importância do corte de wafers
O corte de wafers desempenha um papel crítico no processo de fabricação de semicondutores, impactando diretamente as etapas subsequentes, bem como a qualidade e o desempenho do produto final. Sua importância pode ser detalhada da seguinte forma:
Em primeiro lugar, a precisão e a consistência do corte são essenciais para garantir o rendimento e a confiabilidade do chip. Durante a fabricação, os wafers passam por múltiplas etapas de processamento para formar inúmeras estruturas de circuitos complexos, que devem ser divididos com precisão em chips individuais (matriz). Se houver erros significativos de alinhamento ou corte durante o processo de corte, os circuitos podem ser danificados, afetando a funcionalidade e a confiabilidade do chip. Portanto, a tecnologia de corte de alta precisão não apenas garante a integridade de cada chip, mas também evita danos aos circuitos internos, melhorando a taxa geral de rendimento.
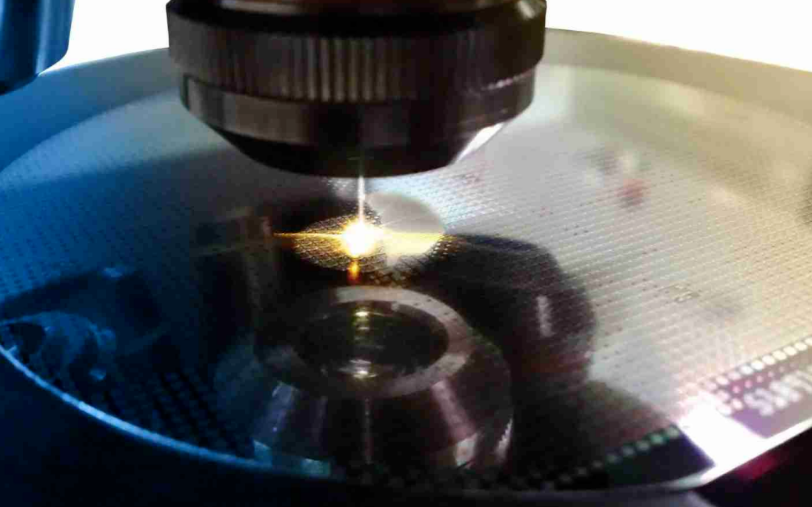
Em segundo lugar, o corte de wafers tem um impacto significativo na eficiência da produção e no controle de custos. Como uma etapa crucial no processo de fabricação, sua eficiência afeta diretamente o progresso das etapas subsequentes. Ao otimizar o processo de corte, aumentar os níveis de automação e melhorar as velocidades de corte, a eficiência geral da produção pode ser significativamente aprimorada.
Por outro lado, o desperdício de material durante o corte em cubos é um fator crítico na gestão de custos. A utilização de tecnologias avançadas de corte em cubos não só reduz perdas desnecessárias de material durante o processo de corte, como também aumenta a utilização de wafers, reduzindo assim os custos de produção.
Com os avanços na tecnologia de semicondutores, os diâmetros dos wafers continuam a aumentar, e as densidades dos circuitos aumentam consequentemente, impondo maiores demandas à tecnologia de corte. Wafers maiores exigem um controle mais preciso dos caminhos de corte, especialmente em áreas de circuitos de alta densidade, onde mesmo pequenos desvios podem resultar em defeitos em vários chips. Além disso, wafers maiores envolvem mais linhas de corte e etapas de processo mais complexas, exigindo melhorias adicionais na precisão, consistência e eficiência das tecnologias de corte para atender a esses desafios.
1.3 Processo de corte em cubos de wafer
O processo de corte em cubos de wafers abrange todas as etapas, desde a preparação até a inspeção final de qualidade, sendo cada etapa crucial para garantir a qualidade e o desempenho dos chips cortados em cubos. Abaixo, uma explicação detalhada de cada fase.
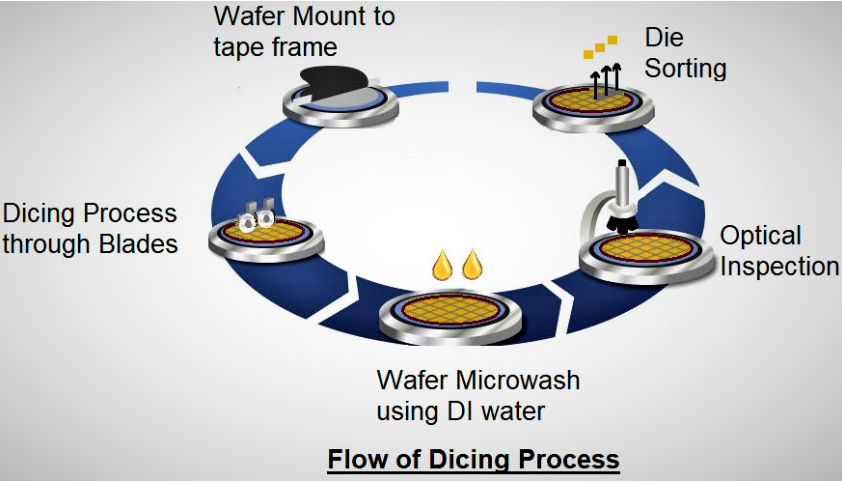
Fase | Descrição detalhada |
Fase de Preparação | -Limpeza de wafers: Use água de alta pureza e agentes de limpeza especializados, combinados com lavagem ultrassônica ou mecânica, para remover impurezas, partículas e contaminantes, garantindo uma superfície limpa. -Posicionamento preciso: Utilize equipamentos de alta precisão para garantir que o wafer seja dividido com precisão ao longo dos caminhos de corte projetados. -Fixação de wafer: Prenda o wafer em uma estrutura de fita para manter a estabilidade durante o corte, evitando danos por vibração ou movimento. |
Fase de Corte | -Corte em cubos com lâmina: Empregue lâminas revestidas de diamante rotativas de alta velocidade para corte físico, adequadas para materiais à base de silício e econômicas. -Corte a laser: Utilize feixes de laser de alta energia para corte sem contato, ideal para materiais frágeis ou de alta dureza, como nitreto de gálio, oferecendo maior precisão e menos perda de material. -Novas tecnologias: Introduzir tecnologias de corte a laser e plasma para melhorar ainda mais a eficiência e a precisão, minimizando as zonas afetadas pelo calor. |
Fase de Limpeza | - Utilize água deionizada (água DI) e agentes de limpeza especializados, combinados com limpeza ultrassônica ou por spray, para remover detritos e poeira gerados durante o corte, evitando que resíduos afetem os processos subsequentes ou o desempenho elétrico do chip. - Água DI de alta pureza evita a introdução de novos contaminantes, garantindo um ambiente de wafer limpo. |
Fase de Inspeção | -Inspeção Óptica: Use sistemas de detecção óptica combinados com algoritmos de IA para identificar defeitos rapidamente, garantindo que não haja rachaduras ou lascas nos chips cortados, melhorando a eficiência da inspeção e reduzindo o erro humano. -Medição de Dimensão: Verifique se as dimensões do chip atendem às especificações do projeto. -Teste de desempenho elétrico: Garantir que o desempenho elétrico de chips críticos atenda aos padrões, garantindo confiabilidade em aplicações subsequentes. |
Fase de triagem | - Utilize braços robóticos ou ventosas a vácuo para separar cavacos qualificados da estrutura da fita e classificá-los automaticamente com base no desempenho, garantindo eficiência e flexibilidade de produção e, ao mesmo tempo, melhorando a precisão. |
O processo de corte de wafers envolve a limpeza, o posicionamento, o corte, a limpeza, a inspeção e a classificação dos wafers, sendo cada etapa crucial. Com os avanços em automação, corte a laser e tecnologias de inspeção por IA, os sistemas modernos de corte de wafers podem alcançar maior precisão, velocidade e menor perda de material. No futuro, novas tecnologias de corte, como laser e plasma, substituirão gradualmente o corte tradicional por lâmina para atender às necessidades de projetos de chips cada vez mais complexos, impulsionando ainda mais o desenvolvimento dos processos de fabricação de semicondutores.
Tecnologia de Corte de Wafer e Seus Princípios
A imagem ilustra três tecnologias comuns de corte de wafers:Corte em cubos com lâmina,Corte a laser, eCorte de Plasma. Abaixo está uma análise detalhada e uma explicação complementar dessas três técnicas:
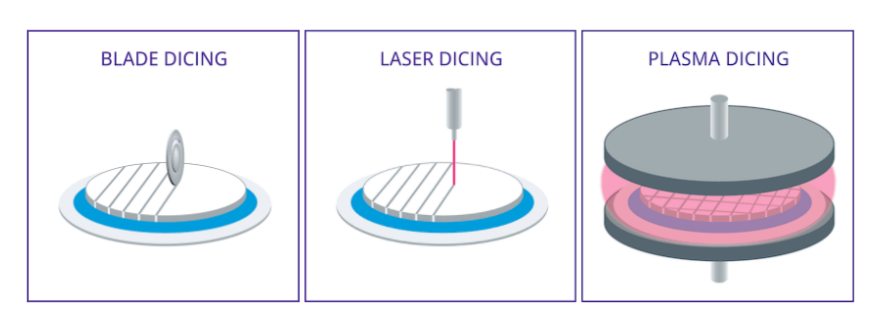
Na fabricação de semicondutores, o corte de wafers é uma etapa crucial que requer a seleção do método de corte apropriado com base na espessura do wafer. O primeiro passo é determinar a espessura do wafer. Se a espessura do wafer exceder 100 mícrons, o corte por lâmina pode ser escolhido como método de corte. Se o corte por lâmina não for adequado, pode-se utilizar o método de corte por fratura, que inclui técnicas de corte por riscagem e corte por lâmina.
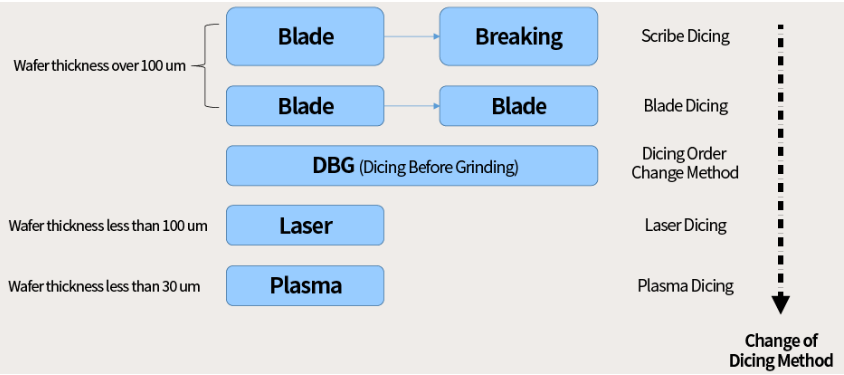
Quando a espessura da lâmina estiver entre 30 e 100 mícrons, recomenda-se o método DBG (Corte Antes da Moagem). Nesse caso, pode-se optar pelo corte por riscagem, corte com lâmina ou ajuste da sequência de corte conforme necessário para obter os melhores resultados.
Para wafers ultrafinos com espessura inferior a 30 mícrons, o corte a laser torna-se o método preferido devido à sua capacidade de cortar wafers finos com precisão, sem causar danos excessivos. Se o corte a laser não atender a requisitos específicos, o corte a plasma pode ser usado como alternativa. Este fluxograma fornece um caminho claro para a tomada de decisão, garantindo a escolha da tecnologia de corte de wafer mais adequada para diferentes condições de espessura.
2.1 Tecnologia de Corte Mecânico
A tecnologia de corte mecânico é o método tradicional de corte de wafers. O princípio básico é usar um rebolo diamantado rotativo de alta velocidade como ferramenta de corte para fatiar o wafer. O equipamento principal inclui um fuso com mancal de ar, que aciona o rebolo diamantado em alta velocidade para realizar cortes ou ranhuras precisos ao longo de um caminho de corte predefinido. Essa tecnologia é amplamente utilizada na indústria devido ao seu baixo custo, alta eficiência e ampla aplicabilidade.
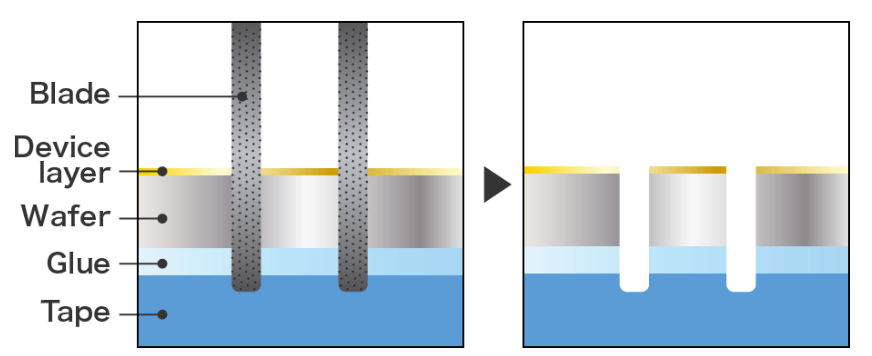
Vantagens
A alta dureza e resistência ao desgaste das ferramentas de rebolo diamantado permitem que a tecnologia de corte mecânico se adapte às necessidades de corte de diversos materiais de wafer, sejam eles materiais tradicionais à base de silício ou semicondutores compostos mais recentes. Sua operação é simples, com requisitos técnicos relativamente baixos, o que promove ainda mais sua popularidade na produção em massa. Além disso, em comparação com outros métodos de corte, como o corte a laser, o corte mecânico tem custos mais controláveis, tornando-o adequado para necessidades de produção em grande escala.
Limitações
Apesar de suas inúmeras vantagens, a tecnologia de corte mecânico também apresenta limitações. Primeiro, devido ao contato físico entre a ferramenta e o wafer, a precisão do corte é relativamente limitada, frequentemente levando a desvios dimensionais que podem afetar a precisão do empacotamento e dos testes subsequentes do chip. Segundo, defeitos como lascamento e rachaduras podem ocorrer facilmente durante o processo de corte mecânico, o que não apenas afeta a taxa de rendimento, mas também pode impactar negativamente a confiabilidade e a vida útil dos chips. Os danos induzidos por estresse mecânico são particularmente prejudiciais para a fabricação de chips de alta densidade, especialmente no corte de materiais frágeis, onde esses problemas são mais proeminentes.
Melhorias tecnológicas
Para superar essas limitações, os pesquisadores estão continuamente otimizando o processo de corte mecânico. As principais melhorias incluem o aprimoramento do design e da seleção de materiais dos rebolos para melhorar a precisão e a durabilidade do corte. Além disso, a otimização do design estrutural e dos sistemas de controle dos equipamentos de corte melhorou ainda mais a estabilidade e a automação do processo de corte. Esses avanços reduzem erros causados por operações humanas e melhoram a consistência dos cortes. A introdução de tecnologias avançadas de inspeção e controle de qualidade para monitoramento em tempo real de anomalias durante o processo de corte também melhorou significativamente a confiabilidade e o rendimento do corte.
Desenvolvimento Futuro e Novas Tecnologias
Embora a tecnologia de corte mecânico ainda ocupe uma posição significativa no corte de wafers, novas tecnologias de corte estão avançando rapidamente à medida que os processos de semicondutores evoluem. Por exemplo, a aplicação da tecnologia de corte a laser térmico oferece novas soluções para os problemas de precisão e defeitos no corte mecânico. Este método de corte sem contato reduz o estresse físico no wafer, diminuindo significativamente a incidência de lascas e rachaduras, especialmente ao cortar materiais mais frágeis. No futuro, a integração da tecnologia de corte mecânico com técnicas de corte emergentes proporcionará à fabricação de semicondutores mais opções e flexibilidade, aprimorando ainda mais a eficiência da fabricação e a qualidade dos chips.
Concluindo, embora a tecnologia de corte mecânico tenha certas desvantagens, as melhorias tecnológicas contínuas e sua integração com novas técnicas de corte permitem que ela ainda desempenhe um papel importante na fabricação de semicondutores e mantenha sua competitividade em processos futuros.
2.2 Tecnologia de corte a laser
A tecnologia de corte a laser, como um novo método de corte de wafers, vem gradualmente ganhando ampla atenção na indústria de semicondutores devido à sua alta precisão, ausência de danos mecânicos por contato e rápida capacidade de corte. Essa tecnologia utiliza a alta densidade de energia e a capacidade de focalização de um feixe de laser para criar uma pequena zona afetada pelo calor na superfície do material do wafer. Quando o feixe de laser é aplicado ao wafer, a tensão térmica gerada causa a fratura do material no local designado, proporcionando um corte preciso.
Vantagens da tecnologia de corte a laser
• Alta Precisão:A capacidade de posicionamento preciso do feixe de laser permite precisão de corte em nível de mícron ou até mesmo nanométrico, atendendo aos requisitos da moderna fabricação de circuitos integrados de alta precisão e alta densidade.
• Sem contato mecânico: O corte a laser evita o contato físico com o wafer, prevenindo problemas comuns no corte mecânico, como lascas e rachaduras, melhorando significativamente a taxa de rendimento e a confiabilidade dos chips.
• Velocidade de corte rápida:A alta velocidade do corte a laser contribui para o aumento da eficiência da produção, tornando-o especialmente adequado para cenários de produção em larga escala e alta velocidade.
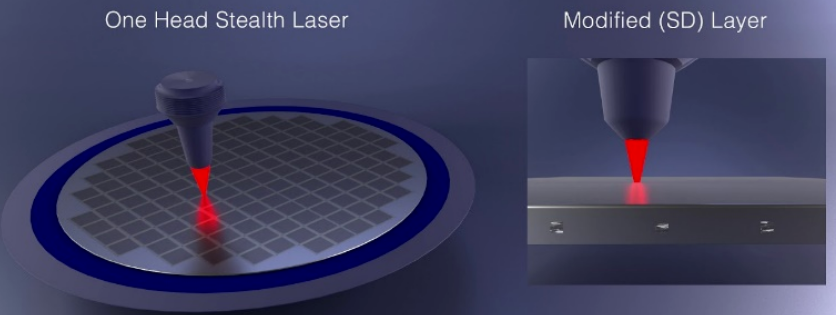
Desafios enfrentados
• Alto custo do equipamento:O investimento inicial em equipamentos de corte a laser é alto, o que representa pressão econômica, especialmente para pequenas e médias empresas de produção.
• Controle de Processos Complexos:O corte a laser exige controle preciso de vários parâmetros, incluindo densidade de energia, posição do foco e velocidade de corte, tornando o processo complexo.
• Problemas na zona afetada pelo calorEmbora a natureza sem contato do corte a laser reduza os danos mecânicos, o estresse térmico causado pela zona afetada pelo calor (ZTA) pode impactar negativamente as propriedades do material do wafer. Uma otimização adicional do processo é necessária para minimizar esse efeito.
Direções de Melhoria Tecnológica
Para enfrentar esses desafios, os pesquisadores estão se concentrando em reduzir os custos dos equipamentos, melhorar a eficiência do corte e otimizar o fluxo do processo.
• Lasers e Sistemas Ópticos Eficientes:Ao desenvolver lasers mais eficientes e sistemas ópticos avançados, é possível reduzir os custos dos equipamentos e, ao mesmo tempo, aumentar a precisão e a velocidade do corte.
• Otimização de Parâmetros de Processo:Pesquisas aprofundadas sobre a interação entre lasers e materiais de wafer estão sendo conduzidas para melhorar processos que reduzem a zona afetada pelo calor, melhorando assim a qualidade do corte.
• Sistemas de Controle Inteligente:O desenvolvimento de tecnologias de controle inteligente visa automatizar e otimizar o processo de corte a laser, melhorando sua estabilidade e consistência.
A tecnologia de corte a laser é particularmente eficaz em wafers ultrafinos e em cenários de corte de alta precisão. À medida que o tamanho dos wafers aumenta e a densidade dos circuitos aumenta, os métodos tradicionais de corte mecânico enfrentam dificuldades para atender às demandas de alta precisão e eficiência da fabricação moderna de semicondutores. Devido às suas vantagens únicas, o corte a laser está se tornando a solução preferida nessas áreas.
Embora a tecnologia de corte a laser ainda enfrente desafios como altos custos de equipamentos e complexidade de processos, suas vantagens únicas em alta precisão e danos sem contato a tornam uma importante direção para o desenvolvimento na fabricação de semicondutores. À medida que a tecnologia a laser e os sistemas de controle inteligentes continuam a avançar, espera-se que o corte a laser melhore ainda mais a eficiência e a qualidade do corte de wafers, impulsionando o desenvolvimento contínuo da indústria de semicondutores.
2.3 Tecnologia de Corte de Plasma
A tecnologia de corte a plasma, como um método emergente de corte de wafers, tem ganhado bastante atenção nos últimos anos. Essa tecnologia utiliza feixes de plasma de alta energia para cortar wafers com precisão, controlando a energia, a velocidade e o caminho de corte do feixe de plasma, alcançando resultados de corte ideais.
Princípio de funcionamento e vantagens
O processo de corte a plasma utiliza um feixe de plasma de alta temperatura e alta energia gerado pelo equipamento. Este feixe pode aquecer o material do wafer até seu ponto de fusão ou vaporização em um tempo muito curto, permitindo um corte rápido. Comparado ao corte mecânico ou a laser tradicional, o corte a plasma é mais rápido e produz uma zona menor afetada pelo calor, reduzindo efetivamente a ocorrência de rachaduras e danos durante o corte.
Em aplicações práticas, a tecnologia de corte a plasma é particularmente adequada para lidar com wafers com formatos complexos. Seu feixe de plasma ajustável e de alta energia pode cortar facilmente wafers de formatos irregulares com alta precisão. Portanto, na fabricação de microeletrônicos, especialmente na produção personalizada e em pequenos lotes de chips de alta qualidade, essa tecnologia demonstra grande potencial para ampla utilização.
Desafios e Limitações
Apesar das muitas vantagens da tecnologia de corte a plasma, ela também enfrenta alguns desafios.
• Processo Complexo:O processo de corte a plasma é complexo e requer equipamentos de alta precisão e operadores experientes para garantirprecisão e estabilidade no corte.
• Controle e Segurança Ambiental:A natureza de alta temperatura e alta energia do feixe de plasma exige rigoroso controle ambiental e medidas de segurança, o que aumenta a complexidade e o custo de implementação.
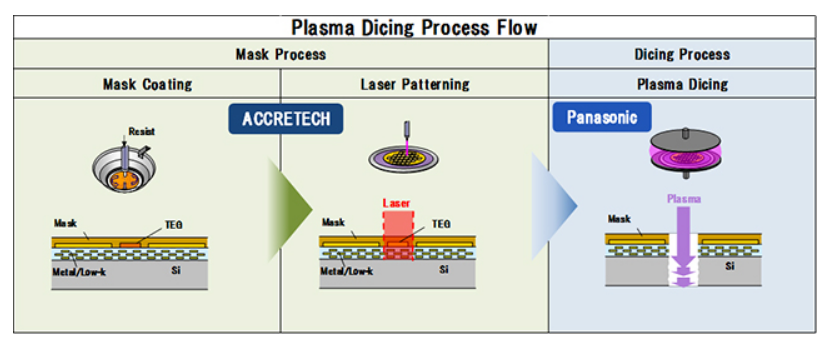
Direções de desenvolvimento futuro
Com os avanços tecnológicos, espera-se que os desafios associados ao corte a plasma sejam gradualmente superados. Desenvolvendo equipamentos de corte mais inteligentes e estáveis, a dependência de operações manuais pode ser reduzida, melhorando assim a eficiência da produção. Ao mesmo tempo, a otimização dos parâmetros do processo e do ambiente de corte ajudará a reduzir os riscos de segurança e os custos operacionais.
Na indústria de semicondutores, as inovações em tecnologia de corte e corte de wafers são cruciais para impulsionar o desenvolvimento do setor. A tecnologia de corte a plasma, com sua alta precisão, eficiência e capacidade de lidar com formatos complexos de wafers, emergiu como um novo e significativo player nesse campo. Embora ainda existam alguns desafios, essas questões serão gradualmente abordadas com a inovação tecnológica contínua, trazendo mais possibilidades e oportunidades para a fabricação de semicondutores.
As perspectivas de aplicação da tecnologia de corte a plasma são vastas e espera-se que ela desempenhe um papel ainda mais importante na fabricação de semicondutores no futuro. Por meio de inovação e otimização tecnológicas contínuas, o corte a plasma não apenas solucionará os desafios existentes, mas também se tornará um poderoso impulsionador do crescimento da indústria de semicondutores.
2.4 Qualidade de corte e fatores de influência
A qualidade do corte do wafer é fundamental para o subsequente empacotamento do chip, os testes e o desempenho e a confiabilidade geral do produto final. Problemas comuns encontrados durante o corte incluem rachaduras, lascas e desvios de corte. Esses problemas são influenciados por diversos fatores que atuam em conjunto.
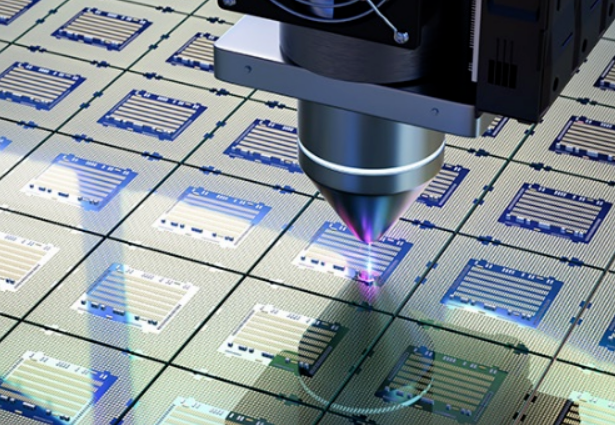
Categoria | Contente | Impacto |
Parâmetros do Processo | A velocidade de corte, a taxa de avanço e a profundidade de corte afetam diretamente a estabilidade e a precisão do processo de corte. Configurações inadequadas podem levar à concentração de tensões e à formação excessiva de zonas afetadas pelo calor, resultando em trincas e lascas. Ajustar os parâmetros adequadamente com base no material do wafer, na espessura e nos requisitos de corte é fundamental para alcançar os resultados de corte desejados. | Os parâmetros de processo corretos garantem um corte preciso e reduzem o risco de defeitos como rachaduras e lascas. |
Fatores de Equipamentos e Materiais | -Qualidade da lâmina: O material, a dureza e a resistência ao desgaste da lâmina influenciam a suavidade do processo de corte e a planura da superfície de corte. Lâminas de baixa qualidade aumentam o atrito e o estresse térmico, podendo causar rachaduras ou lascas. A escolha do material correto da lâmina é crucial. -Desempenho do líquido de arrefecimento: Os fluidos de arrefecimento ajudam a reduzir a temperatura de corte, minimizar o atrito e remover detritos. Um fluido de arrefecimento ineficaz pode levar a altas temperaturas e acúmulo de detritos, impactando a qualidade e a eficiência do corte. Selecionar fluidos de arrefecimento eficientes e ecologicamente corretos é vital. | A qualidade da lâmina afeta a precisão e a suavidade do corte. A refrigeração inadequada pode resultar em baixa qualidade e eficiência de corte, destacando a necessidade do uso otimizado da refrigeração. |
Controle de Processos e Inspeção de Qualidade | -Controle de Processo: Monitoramento e ajuste em tempo real dos principais parâmetros de corte para garantir estabilidade e consistência no processo de corte. -Inspeção de Qualidade: Verificações de aparência pós-corte, medições dimensionais e testes de desempenho elétrico ajudam a identificar e resolver problemas de qualidade prontamente, melhorando a precisão e a consistência do corte. | O controle adequado do processo e a inspeção de qualidade ajudam a garantir resultados de corte consistentes e de alta qualidade, além da detecção precoce de possíveis problemas. |

Melhorando a qualidade do corte
Aprimorar a qualidade do corte requer uma abordagem abrangente que leve em consideração os parâmetros do processo, a seleção de equipamentos e materiais, o controle do processo e a inspeção. Refinando continuamente as tecnologias de corte e otimizando os métodos de processo, a precisão e a estabilidade do corte de wafers podem ser ainda mais aprimoradas, proporcionando um suporte técnico mais confiável para a indústria de fabricação de semicondutores.
#03 Manuseio e Teste Pós-Corte
3.1 Limpeza e Secagem
As etapas de limpeza e secagem após o corte do wafer são cruciais para garantir a qualidade do chip e o bom andamento dos processos subsequentes. Durante essa etapa, é essencial remover completamente os resíduos de silício, resíduos de refrigerante e outros contaminantes gerados durante o corte. É igualmente importante garantir que os chips não sejam danificados durante o processo de limpeza e, após a secagem, garantir que não haja umidade na superfície do chip para evitar problemas como corrosão ou descarga eletrostática.
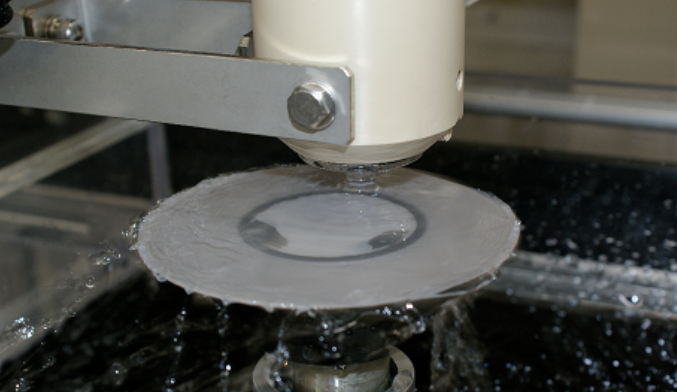
Manuseio pós-corte: processo de limpeza e secagem
Etapa do processo | Contente | Impacto |
Processo de limpeza | -Método: Utilize agentes de limpeza especializados e água pura, combinados com técnicas de escovação ultrassônica ou mecânica para limpeza. | Garante a remoção completa de contaminantes e evita danos aos chips durante a limpeza. |
-Seleção de Agente de Limpeza: Escolha com base no material do wafer e no tipo de contaminante para garantir uma limpeza eficaz sem danificar o chip. | A seleção adequada do agente é essencial para uma limpeza eficaz e proteção contra cavacos. | |
-Controle de Parâmetros: Controle rigorosamente a temperatura, o tempo e a concentração da solução de limpeza para evitar problemas de qualidade causados por limpeza inadequada. | Os controles ajudam a evitar danos ao wafer ou deixar contaminantes para trás, garantindo uma qualidade consistente. | |
Processo de secagem | -Métodos Tradicionais: Secagem ao ar natural e secagem ao ar quente, que têm baixa eficiência e podem levar ao acúmulo de eletricidade estática. | Pode resultar em tempos de secagem mais lentos e potenciais problemas estáticos. |
-Tecnologias modernas: Use tecnologias avançadas, como secagem a vácuo e secagem infravermelha, para garantir que os chips sequem rapidamente e evitar efeitos nocivos. | Processo de secagem mais rápido e eficiente, reduzindo riscos de descarga estática ou problemas relacionados à umidade. | |
Seleção e Manutenção de Equipamentos | -Seleção de equipamentos: Máquinas de limpeza e secagem de alto desempenho melhoram a eficiência do processamento e controlam com precisão possíveis problemas durante o manuseio. | Máquinas de alta qualidade garantem melhor processamento e reduzem a probabilidade de erros durante a limpeza e a secagem. |
-Manutenção de Equipamentos: A inspeção e manutenção regulares do equipamento garantem que ele permaneça em ótimas condições de funcionamento, garantindo a qualidade do chip. | A manutenção adequada evita falhas nos equipamentos, garantindo um processamento confiável e de alta qualidade. |
Limpeza e secagem pós-corte
As etapas de limpeza e secagem após o corte do wafer são processos complexos e delicados que exigem a consideração cuidadosa de diversos fatores para garantir o resultado final do processamento. Utilizando métodos científicos e procedimentos rigorosos, é possível garantir que cada chip chegue às etapas subsequentes de embalagem e teste em condições ideais.
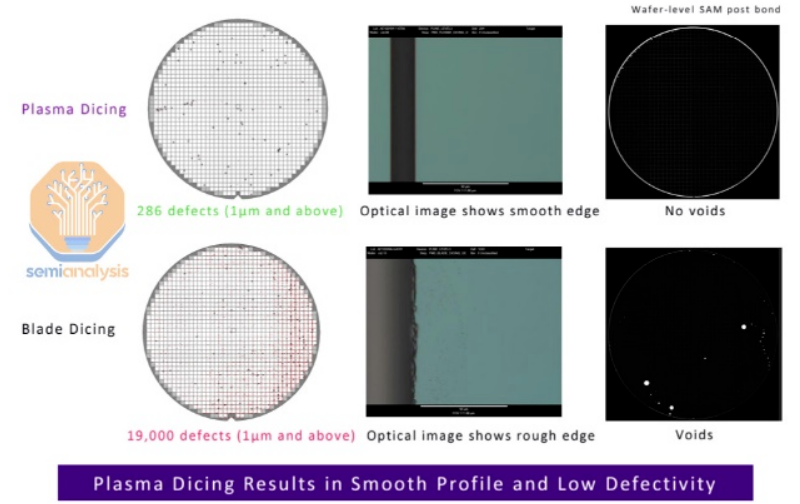
Inspeção e teste pós-corte
Etapa | Contente | Impacto |
Etapa de inspeção | 1.Inspeção Visual: Utilize equipamentos de inspeção visual ou automatizada para verificar defeitos visíveis, como rachaduras, lascas ou contaminação na superfície do cavaco. Identifique rapidamente cavacos fisicamente danificados para evitar desperdícios. | Ajuda a identificar e eliminar cavacos defeituosos no início do processo, reduzindo a perda de material. |
2.Medidas de tamanho: Use dispositivos de medição de precisão para medir com exatidão as dimensões dos chips, garantindo que o tamanho do corte atenda às especificações do projeto e evitando problemas de desempenho ou dificuldades de embalagem. | Garante que os chips estejam dentro dos limites de tamanho exigidos, evitando degradação de desempenho ou problemas de montagem. | |
3.Teste de desempenho elétrico: Avalie os principais parâmetros elétricos, como resistência, capacitância e indutância, para identificar chips não compatíveis e garantir que apenas chips com desempenho qualificado avancem para o próximo estágio. | Garante que apenas chips funcionais e com desempenho testado avancem no processo, reduzindo o risco de falhas em estágios posteriores. | |
Etapa de teste | 1.Teste Funcional: Verificar se a funcionalidade básica do chip funciona conforme o esperado, identificando e eliminando chips com anormalidades funcionais. | Garante que os chips atendam aos requisitos operacionais básicos antes de avançar para estágios posteriores. |
2.Teste de confiabilidade: Avalie a estabilidade do desempenho do chip sob uso prolongado ou em ambientes adversos, geralmente envolvendo envelhecimento em alta temperatura, testes em baixa temperatura e testes de umidade para simular condições extremas do mundo real. | Garante que os chips possam funcionar de forma confiável em diversas condições ambientais, melhorando a longevidade e a estabilidade do produto. | |
3.Teste de compatibilidade: Verifique se o chip funciona corretamente com outros componentes ou sistemas, garantindo que não haja falhas ou degradação de desempenho devido à incompatibilidade. | Garante uma operação suave em aplicações do mundo real, evitando problemas de compatibilidade. |
3.3 Embalagem e Armazenamento
Após o corte do wafer, os chips são um produto crucial do processo de fabricação de semicondutores, e suas etapas de embalagem e armazenamento são igualmente importantes. Medidas adequadas de embalagem e armazenamento são essenciais não apenas para garantir a segurança e a estabilidade dos chips durante o transporte e o armazenamento, mas também para fornecer um suporte sólido para as etapas subsequentes de produção, teste e embalagem.
Resumo das etapas de inspeção e teste:
As etapas de inspeção e teste de chips após o corte do wafer abrangem uma série de aspectos, incluindo inspeção visual, medição de tamanho, testes de desempenho elétrico, testes funcionais, testes de confiabilidade e testes de compatibilidade. Essas etapas são interligadas e complementares, formando uma barreira sólida para garantir a qualidade e a confiabilidade do produto. Por meio de procedimentos rigorosos de inspeção e teste, potenciais problemas podem ser identificados e resolvidos prontamente, garantindo que o produto final atenda aos requisitos e expectativas do cliente.
Aspecto | Contente |
Medidas de embalagem | 1.Antiestático: Os materiais de embalagem devem ter excelentes propriedades antiestáticas para evitar que a eletricidade estática danifique os dispositivos ou afete seu desempenho. |
2.À prova de umidade: Os materiais de embalagem devem ter boa resistência à umidade para evitar corrosão e deterioração do desempenho elétrico causadas pela umidade. | |
3.À prova de choque: Os materiais de embalagem devem fornecer absorção de choque eficaz para proteger os chips de vibração e impacto durante o transporte. | |
Ambiente de armazenamento | 1.Controle de umidade: Controle rigorosamente a umidade dentro de uma faixa apropriada para evitar absorção de umidade e corrosão causadas por umidade excessiva ou problemas estáticos causados por baixa umidade. |
2.Limpeza: Mantenha um ambiente de armazenamento limpo para evitar contaminação dos chips por poeira e impurezas. | |
3.Controle de temperatura: Defina uma faixa de temperatura razoável e mantenha a estabilidade da temperatura para evitar envelhecimento acelerado devido ao calor excessivo ou problemas de condensação causados por baixas temperaturas. | |
Inspeção regular | Inspecione e avalie regularmente os chips armazenados, utilizando inspeções visuais, medições de tamanho e testes de desempenho elétrico para identificar e solucionar possíveis problemas em tempo hábil. Com base no tempo e nas condições de armazenamento, planeje o uso dos chips para garantir que sejam utilizados em condições ideais. |
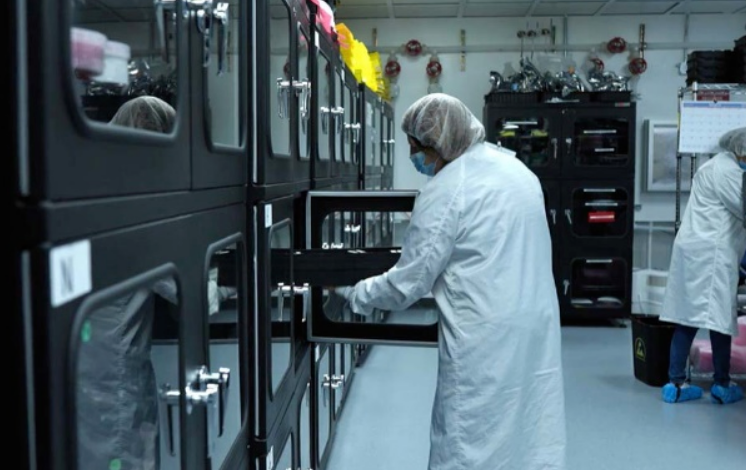
O problema de microfissuras e danos durante o processo de corte do wafer é um desafio significativo na fabricação de semicondutores. O estresse de corte é a principal causa desse fenômeno, pois cria pequenas rachaduras e danos na superfície do wafer, levando ao aumento dos custos de fabricação e à redução da qualidade do produto.
Para enfrentar esse desafio, é crucial minimizar o estresse de corte e implementar técnicas, ferramentas e condições de corte otimizadas. A atenção cuidadosa a fatores como material da lâmina, velocidade de corte, pressão e métodos de resfriamento pode ajudar a reduzir a formação de microfissuras e melhorar o rendimento geral do processo. Além disso, pesquisas em andamento sobre tecnologias de corte mais avançadas, como o corte a laser, estão explorando maneiras de mitigar ainda mais esses problemas.
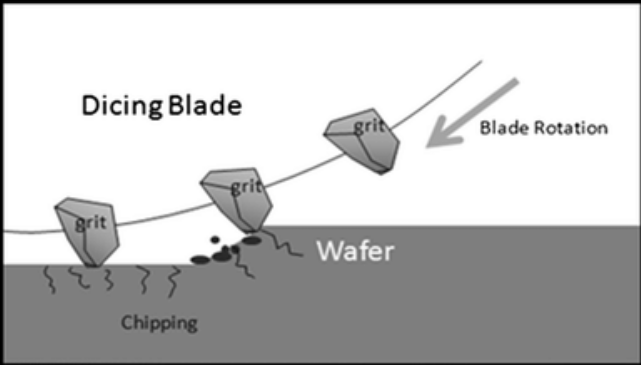
Por serem materiais frágeis, os wafers são propensos a alterações estruturais internas quando submetidos a tensões mecânicas, térmicas ou químicas, levando à formação de microfissuras. Embora essas fissuras possam não ser imediatamente perceptíveis, elas podem se expandir e causar danos mais severos à medida que o processo de fabricação avança. Esse problema se torna especialmente problemático durante as etapas subsequentes de embalagem e teste, onde flutuações de temperatura e tensões mecânicas adicionais podem fazer com que essas microfissuras evoluam para fraturas visíveis, potencialmente levando à falha do chip.
Para mitigar esse risco, é essencial controlar cuidadosamente o processo de corte, otimizando parâmetros como velocidade, pressão e temperatura. O uso de métodos de corte menos agressivos, como o corte a laser, pode reduzir o estresse mecânico no wafer e minimizar a formação de microfissuras. Além disso, a implementação de métodos avançados de inspeção, como varredura infravermelha ou imagens de raios X durante o processo de corte do wafer, pode ajudar a detectar essas rachaduras em estágio inicial antes que causem maiores danos.
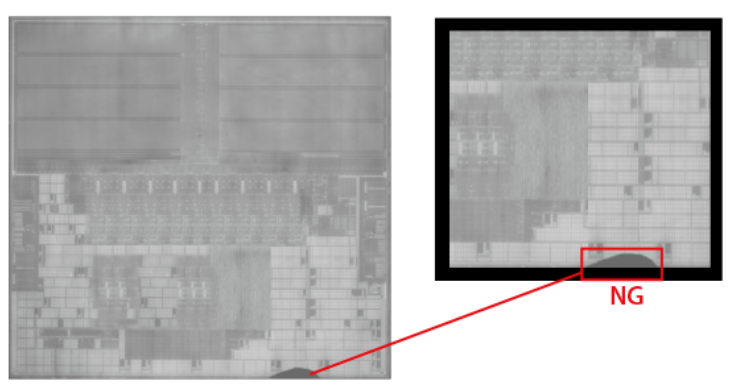
Danos à superfície do wafer são uma preocupação significativa no processo de corte, pois podem ter um impacto direto no desempenho e na confiabilidade do chip. Esses danos podem ser causados pelo uso inadequado de ferramentas de corte, parâmetros de corte incorretos ou defeitos de material inerentes ao próprio wafer. Independentemente da causa, esses danos podem levar a alterações na resistência elétrica ou na capacitância do circuito, afetando o desempenho geral.
Para abordar essas questões, duas estratégias principais estão sendo exploradas:
1. Otimização de ferramentas de corte e parâmetros: Ao usar lâminas mais afiadas, ajustar a velocidade de corte e modificar a profundidade do corte, a concentração de estresse durante o processo de corte pode ser minimizada, reduzindo assim o potencial de danos.
2. Explorando novas tecnologias de corteTécnicas avançadas como corte a laser e corte a plasma oferecem maior precisão, reduzindo potencialmente o nível de danos causados ao wafer. Essas tecnologias estão sendo estudadas para encontrar maneiras de alcançar alta precisão de corte, minimizando o estresse térmico e mecânico no wafer.
Área de Impacto Térmico e Seus Efeitos no Desempenho
Em processos de corte térmico, como corte a laser e plasma, altas temperaturas inevitavelmente criam uma zona de impacto térmico na superfície do wafer. Essa área, onde o gradiente de temperatura é significativo, pode alterar as propriedades do material, afetando o desempenho final do chip.
Impacto da Zona Térmica Afetada (ZTA):
Mudanças na estrutura cristalina: Sob altas temperaturas, os átomos dentro do material do wafer podem se rearranjar, causando distorções na estrutura cristalina. Essa distorção enfraquece o material, reduzindo sua resistência mecânica e estabilidade, o que aumenta o risco de falha do chip durante o uso.
Mudanças nas propriedades elétricasAltas temperaturas podem alterar a concentração e a mobilidade dos portadores em materiais semicondutores, afetando a condutividade elétrica e a eficiência da transmissão de corrente do chip. Essas alterações podem levar a uma queda no desempenho do chip, tornando-o potencialmente inadequado para a finalidade pretendida.
Para mitigar esses efeitos, controlar a temperatura durante o corte, otimizar os parâmetros de corte e explorar métodos como jatos de resfriamento ou tratamentos pós-processamento são estratégias essenciais para reduzir a extensão do impacto térmico e manter a integridade do material.
De modo geral, tanto microfissuras quanto zonas de impacto térmico representam desafios cruciais na tecnologia de corte de wafers. Pesquisas contínuas, juntamente com avanços tecnológicos e medidas de controle de qualidade, serão necessárias para aprimorar a qualidade dos produtos semicondutores e aumentar sua competitividade no mercado.
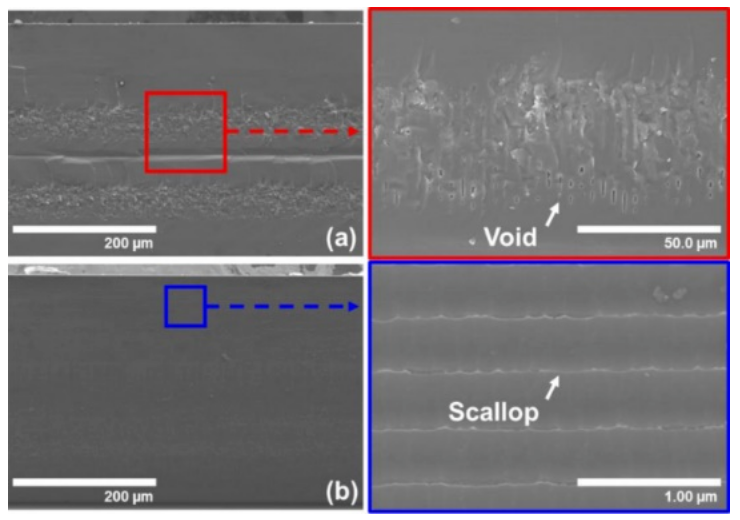
Medidas para controlar a zona de impacto térmico:
Otimizando os Parâmetros do Processo de Corte: Reduzir a velocidade e a potência de corte pode minimizar efetivamente o tamanho da zona de impacto térmico (ZTA). Isso ajuda a controlar a quantidade de calor gerada durante o processo de corte, o que impacta diretamente as propriedades do material do wafer.
Tecnologias avançadas de resfriamento: A aplicação de tecnologias como resfriamento por nitrogênio líquido e resfriamento microfluídico pode limitar significativamente o alcance da zona de impacto térmico. Esses métodos de resfriamento ajudam a dissipar o calor com mais eficiência, preservando assim as propriedades do material do wafer e minimizando os danos térmicos.
Seleção de materiaisPesquisadores estão explorando novos materiais, como nanotubos de carbono e grafeno, que possuem excelente condutividade térmica e resistência mecânica. Esses materiais podem reduzir a zona de impacto térmico e, ao mesmo tempo, melhorar o desempenho geral dos chips.
Em resumo, embora a zona de impacto térmico seja uma consequência inevitável das tecnologias de corte térmico, ela pode ser controlada de forma eficaz por meio de técnicas de processamento otimizadas e seleção de materiais. Pesquisas futuras provavelmente se concentrarão no ajuste fino e na automação dos processos de corte térmico para obter um corte de wafers mais eficiente e preciso.

Estratégia de equilíbrio:
Alcançar o equilíbrio ideal entre o rendimento do wafer e a eficiência da produção é um desafio constante na tecnologia de corte de wafers. Os fabricantes precisam considerar múltiplos fatores, como demanda do mercado, custos de produção e qualidade do produto, para desenvolver uma estratégia de produção racional e parâmetros de processo. Ao mesmo tempo, a introdução de equipamentos de corte avançados, o aprimoramento das habilidades dos operadores e o aprimoramento do controle de qualidade da matéria-prima são essenciais para manter ou até mesmo melhorar o rendimento, aumentando a eficiência da produção.
Desafios e oportunidades futuros:
Com o avanço da tecnologia de semicondutores, o corte de wafers enfrenta novos desafios e oportunidades. À medida que o tamanho dos chips diminui e a integração aumenta, as demandas por precisão e qualidade de corte aumentam significativamente. Simultaneamente, tecnologias emergentes oferecem novas ideias para o desenvolvimento de técnicas de corte de wafers. Os fabricantes devem permanecer atentos à dinâmica do mercado e às tendências tecnológicas, ajustando e otimizando continuamente as estratégias de produção e os parâmetros do processo para atender às mudanças do mercado e às demandas tecnológicas.
Concluindo, ao integrar considerações de demanda de mercado, custos de produção e qualidade do produto, e ao introduzir equipamentos e tecnologias avançadas, aprimorando as habilidades dos operadores e fortalecendo o controle da matéria-prima, os fabricantes podem alcançar o melhor equilíbrio entre rendimento do wafer e eficiência de produção durante o corte do wafer, levando à produção eficiente e de alta qualidade de produtos semicondutores.
Perspectivas futuras:
Com os rápidos avanços tecnológicos, a tecnologia de semicondutores avança a um ritmo sem precedentes. Como etapa crucial na fabricação de semicondutores, a tecnologia de corte de wafers está pronta para novos desenvolvimentos empolgantes. Olhando para o futuro, espera-se que a tecnologia de corte de wafers alcance melhorias significativas em precisão, eficiência e custo, injetando nova vitalidade ao crescimento contínuo da indústria de semicondutores.
Aumento da precisão:
Na busca por maior precisão, a tecnologia de corte de wafers desafiará continuamente os limites dos processos existentes. Ao estudar profundamente os mecanismos físicos e químicos do processo de corte e controlar com precisão os parâmetros de corte, serão obtidos resultados de corte mais precisos para atender aos requisitos de projeto de circuitos cada vez mais complexos. Além disso, a exploração de novos materiais e métodos de corte aumentará significativamente o rendimento e a qualidade.
Melhorando a eficiência:
Os novos equipamentos de corte de wafers se concentrarão em design inteligente e automatizado. A introdução de sistemas de controle e algoritmos avançados permitirá que os equipamentos ajustem automaticamente os parâmetros de corte para atender a diferentes materiais e requisitos de design, melhorando significativamente a eficiência da produção. Inovações como a tecnologia de corte multiwafer e os sistemas de troca rápida de lâminas desempenharão um papel crucial no aumento da eficiência.
Redução de custos:
A redução de custos é uma direção fundamental para o desenvolvimento da tecnologia de corte de wafers. À medida que novos materiais e métodos de corte são desenvolvidos, espera-se que os custos com equipamentos e as despesas de manutenção sejam controlados de forma eficaz. Além disso, a otimização dos processos de produção e a redução das taxas de refugo reduzirão ainda mais o desperdício durante a fabricação, levando a uma redução nos custos gerais de produção.
Manufatura Inteligente e IoT:
A integração das tecnologias de manufatura inteligente e Internet das Coisas (IoT) trará mudanças transformadoras para a tecnologia de corte de wafers. Por meio da interconectividade e do compartilhamento de dados entre dispositivos, cada etapa do processo de produção pode ser monitorada e otimizada em tempo real. Isso não apenas melhora a eficiência da produção e a qualidade do produto, como também proporciona às empresas previsões de mercado mais precisas e suporte à tomada de decisões.
No futuro, a tecnologia de corte de wafers proporcionará avanços notáveis em precisão, eficiência e custo. Esses avanços impulsionarão o desenvolvimento contínuo da indústria de semicondutores e trarão mais inovações tecnológicas e conveniências para a sociedade.
Horário da publicação: 19/11/2024